01 Apr Butterfly Valve Introduction Guide
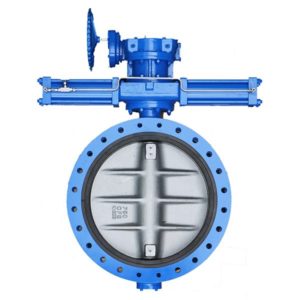
The invention of the butterfly valve has allowed for the improvement of processes and applications in various industries. This introductory guide is intended to familiarize you with what a butterfly valve is, how it works, and its design variations.
What is a Butterfly Valve?
A butterfly valve is a mechanism that regulates the flow of materials within large pipe diameters by the quarter-turn rotation of a disc.
A rod feeds through the center of a disc and this rod is connected to an actuator that controls the motion of the disc. The disc position is either parallel or perpendicular to the flow of media. A butterfly valve differs from other valves because the disc is always in the flow causing a pressure change for any position of the valve.
Sound systems rely on dependable valves. Our butterfly control valve selection is made up of disc valves perfectly sized for various applications and made in precise accordance with industry standards. Find the best butterfly valve for your specific operation by browsing our products page. For custom parts, refer to our request a quote page.
Why is it Called a Butterfly Valve?
Some valves are named for their shape such as ball valve, globe valve, needle valve, etc. Other valves are named for their movement and function – gate valve, plug valve, pinch valve, life valve, slide valve, etc. A butterfly control valve is also named for the movement it makes.
The butterfly valve gets its name from how the movement is similar to a wing for flight. The rod is analogous to a butterfly’s body, while the disc moves like a butterfly wing. A butterfly valve’s motion is similar to that of a butterfly that has landed with the wings moved up and down with a 90-degree motion.
What is a Butterfly Valve Used For?
A butterfly valve regulates flow by starting, slowing, or stopping media. The disk opens and closes with a low-torque rotation of 90 degrees and works for any compatible application. Because they cost less and are lighter weight, the butterfly valve is often preferred over other types of valves.
For some processes, extreme temperatures and corrosion are factors that would easily compromise a valve’s seal. The butterfly valve withstands extreme cold or extreme heat. This means the seal maintains its integrity which is critical for high-stakes applications such as energy production and petroleum processing (as one leak could threaten public safety or the environment).
Principle of Operation
The butterfly valve is classified as a quarter-turn valve. It works like a ball valve for quick shutoff, but unlike a ball valve, the butterfly valve can also open and close incrementally. This difference means that the disc is always present in the flow and allows for a drop in pressure.
This disc is mounted at the center of the pipe. Disc movement is controlled by a rod inserted through the disc and an actuator, located outside the valve. Turning the actuator positions the disc either perpendicular or parallel to the flow.
Where is the Butterfly Valve Located?
For butterfly valve parts orientation, there are some standard guidelines. The butterfly valve needs some distance from other parts such as pumps, elbows, and other valves – 6 pipe diameter separation is ideal.
Usually, the butterfly valve is installed with the valve stem oriented vertically with the actuator directly above it, but in some cases, the stem is situated horizontally instead. When connected to a pump or check valve, there must be clearance for the disc, so it doesn’t interfere with other parts nearby.
3 Main Butterfly Valve Types
While these valves all do essentially the same function, there are variations of butterfly valve design to suit different operations. Below are the three main butterfly valve types.
Zero-offset Butterfly Valve
“Concentric” or “rubber seated” are other names for the zero-offset design. Zero-offset means there is no offset by the stem of the valve. The valve seals via interference along the disc edge at the stem between the disc and the rubber seat.
The rubber seated valve has the lowest pressure rating (up to 250 PSI) and withstands heat up to 400°F. Its rubber seat encases the body to prevent contact with the material which maintains the purity of the media.
High-Performance Double Offset Butterfly Valve
This butterfly valve is referred to as a double offset because the offset is in two places: at the line of the disc seat /body seal, and at the bore. Off-center positioning increases durability for the seal. High-performance valves tolerate pressure up to 1440 PSI and temps up to 1200°F.
A cam-action occurs from the stem being behind the disc as it rubs against the during rotation at 90° for the first 10 degrees of opening, but also for the 10 degrees of closing.
Triple Offset Butterfly Valve
The best type of butterfly valve for high-pressure systems is the triple offset butterfly valve. Of the three types, the triple offset is the most advanced with lower emissions and is designed to work with various environments. Its heat tolerance is 1200°F as it can withstand 1,480 PSI of pressure.
Like the double offset valve, the triple offset valve consists of two offsets situated in the center, but with a third offset having cam action with right-angled conical sealing. It is frictionless and long-wearing by the metal seal components not making contact until their final point.
Common Butterfly Valve Applications
Some processes need more tolerant and wear-resistant valves with special features. Below are some common applications that rely on the unique mechanisms of a butterfly control valve.
Food Processing
Simple design, high durability, and low maintenance are the features needed to regulate fluid flow in any piping system. Certified Food Grade Seat is best for the Food Processing sector, so a White seat is preferred.
While standard resilient seated valves are not 3A approved, there are many on the market that maintain sanitary connections inside and outside. The body material for the valve can range from Epoxy coated iron to Nylon 11 coated iron to Bronze, 304SS, and 316SS.
Refineries
The butterfly valve is commonly found in refineries. These would typically use the more “high end” High-Performance valve with Steel Bodies, or the Triple Offset design that is “Fire Safe” and bubble tight. Many applications involving water use the resiliently seated version.
Shut Off Valves
A butterfly valve is often the best choice as a general shut-off valve above 1.5”-148”. Their simple design allows them to take up less space and less weight than other types of valves. These valves provide a tighter seal than a gate of globe valve and are usually bubble tight. This is most useful when trying to stop the fluid flow as it prevents any fluid from passing through the pipe when closed.
Ship Building
Because of their high durability in saltwater, butterfly valves are commonly used in ships where ABS-approved materials are selected. This type of valve effectively creates a water-tight shutoff in the piping system of a ship to prevent any flow in the pipe. Their small size also allows them to be used in those tight spaces that are common aboard the ship.
They can be used for “jack up” rigs, ballast systems, ship side, and many other applications. Fire Safe approved valves are also necessary for many applications. Additional capabilities are automation and pneumatic function (“closed-loop” pneumatic underwater, electric, and hydraulic).
Be sure to use valves with an ISO-5211 mounting pad and stem. This way it’s easier to get a drop-in replacement at any port. Also, be wary of valves that just have an ISO-5211 mounting pad as the stems are often manufacturer’s “special.”
Sorry, the comment form is closed at this time.