25 Mar Dual Plate Check Valve
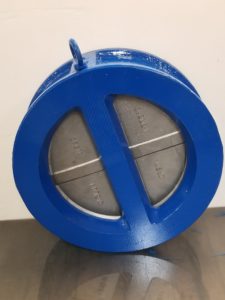
DESCRIPTION
About Dual Plate Check Valves
A check valve is used to automatically open when media flows and then close when fluids flow backward. A check valve is also referred to as a one-way valve, a non-return valve, or a clack valve. Check valves have the ability to pass fluid in a single direction. Safety applications rely on this feature along with the capability to prevent overflow.
The “slamming effect” is characteristic of check valves caused by a sudden stoppage of the pump that causes forward-moving fluid to flow backward rapidly. As the media flows backward, it becomes blocked as it makes contact with the check valve that needs to close. It is called a “slamming effect” because of the noise it makes.
Compared to other check valves, two types of valves close rapidly or slowly: dual plate check valves or swing check valves. Because of its low slamming effect, the dual plate type of check valves is more widely used in certain regions since they have a low slamming effect.
- With the halting of fluid reversal, check valves protect mechanical components in a piping system.
- Should a pipe break, a dual plate control valve prevents a major backflow. This mechanism also reduces energy consumption wastes by preventing backflow to a lower pressure.
- Wafer-type valves have excellent hydrodynamic properties.
- Being lighter in weight benefits installation, transport, and storage.
- Dual plate check valves are suitable for liquid, gas, and steam operations as with heating, air conditioning, and cooling systems.
- They are sometimes found in steam and condensate system applications such as water supply, or pipes for oil and natural gas.
Dual Plate Check Valve Specifications
The dual check valve is one of many check valve types. When selecting a check valve for process flow control, it’s important to familiarize yourself with the specifications. This helps ensure you get the right one for the application.
- Size : 40mm-1200mm(1.5”~48”)
- Pressure testing as according to ISO 5208:
- Seat testing : 11bar (160psi.)
- Body testing : 15bar (220psi.)
- ANSI CLASS 150LB/ PN10
- End connections:
- BS 10 TABLE “E”. ANSI 150LB, ISO-PN. JIS 10K
- Model No. CV-123A (wafer type)
- Size: 1.5″-60″ (40mm-1500mm)
- End Facing FF/RF/RTJ
- Model No. CV-123B (lugged type)
- Size: 1.5″-36″ (40mm-900mm)
- End Facing FF/RF
- Model No. CV-123C (flanged type)
- Size: 1.5″-36″ (40mm-900mm)
- End Facing FF/RF
- Pressure Rating
- CL 125, CL 150, CL 300, CL 600
- PN10, PN16, PN20, PN25, PN40, PN50
- 5K, 10K, 20K
- Thickness: API 594, Maker Standard.
- Design: API 594, Maker Standard.
- Face to Face: API 594, API 6D, ISO 5752, EN 558-1
- Marking: MSS-SP 44
- Flanged Face Standard: MSS-SP 6, ASME B16.1, ASME B16.5, ISO 468
- Inspection Standard: API 598, ISO 5208.
Get more information here about the dual plate check valves (CV-122 and CV-123 series)
Contact Us Today and Receive a Quote for Our Dual Plate Check Valves
Our CV-122 dual plate check valve model is a general-purpose one-way flow valve. Compared to swing valves, dual plate check valves are quick vertical and horizontal, bubble tight, stronger, lighter, smaller, and more reliable compared to the average swing check valves.
Maintenance of the dual plate check valve between flanges is easier due to its lighter weight and short face-to-face dimension. If you need a check valve for fluid control and have concerns about the “slamming effect,” the dual plate check valve is the right choice.
Not sure which check valve is the best for your applications? Contact us today for a customized quote.
Sorry, the comment form is closed at this time.