07 Jul What is the Difference Between Resilient Seated, High Performance, and Triple Offset Butterfly Valves?
For many processes that involve fluid material moving through pipe systems, butterfly valves are needed to stop or regulate flow. With this mechanism, a circular disc is designed to move perpendicular to the passage from fully closed to fully open or anywhere in between. It’s somewhat like a dimming switch. From full light the user can turn the lights down or completely off at the desired speed and vice versa.
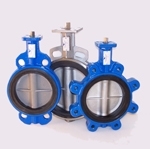
Because of the many applications, designs are varied for the different types of butterfly valves. Pressure, heat, the potential for fire damage, precise operation, and longevity all factor into how a butterfly valve is manufactured to fit within a system.
The key differences between these are the location of the actuating system (the offset) and the material used to make the butterfly valve. Materials such as light alloy, aluminum, or PVC plastic are used for short-term or lower demand applications. Such materials aren’t enough to stand up to heavy-duty operations and require stronger construction.
Learning about the particular design and function of these butterfly valve types allows you to understand how they are similar yet distinctive.
Resilient Seated Butterfly Valve
Resilient seated butterfly valves are the zero offset sort with no offset near the stem. It’s also referred to as “concentric” and “rubber seated.” They handle liquid and gas application demands of up to 400°F in heat or pressure up to 250 PSI.
What makes the valve centric is placement of all the pieces in the center. There is no offset in the body of the valve nor a stem packing adjustment. It operates with 360º rotation of the disc around the center axis. Sealing is made via the interference fit between the disc and the rubber seat at the stem and along the disc edge.
Unlike an offset seated butterfly valve, the rubber seat covering the body ensures that the valve body does not come in contact with the material passing through the pipe. This helps the production contents stay pure and isolated from the body thus allowing less expensive body material. Depending on the conditions of the operations, the rubber may wear out and weaken the sealing function.
Valve Applications
The resilient seated butterfly valve is used to start, stop, and regulate the flow of fluids through pipelines.
It’s suitable for:
- The pharmaceutical, chemical and food industries
- Water and Wastewater applications
- Fire protection systems
- Gas supply
- Low pressure steam
High-Performance Butterfly Valve
The high performance butterfly valve is a double offset configuration (or triple offset to be discussed later on). These are designed to withstand temperatures of up to 1200°F or pressure up to 1440 PSI.
Seat displacement occurs with a primary and secondary offset.
- Offset between the shaft and the centerline of the disc seat and body seal.
- Then offset from the centerline of the bore.
Unlike the zero offset design described above, the double offset butterfly valve’s stem is situated behind the disc to create a cam action. It “rubs” over the seat only at a 90° rotation for the beginning 10 degrees of opening, and ending 10 degrees of closing.
Having the discs arranged and positioned off the center of the pipe bore increases durability for sealing function.
Such metals as Stellite or reinforced Teflon are used for the seat rather than rubber to better sustain regular exposure to high temperatures or pressure..
Valve Applications
Like the resilient seated butterfly valve, the double offset high-performance butterfly valve is also used to start, stop, and regulate fluid movement. However, these are designed for longevity and are more expensive.
Such demanding processes are:
- Water/wastewater treatment
- Chemical processes
- Oil and gas (chemical, petrochemical, and offshore)
- Power generation
- Shipbuilding
- HVAC
- Pulp and paper
- Higher pressure steam
Triple Offset Butterfly Valve
The other type of high performance valves is the triple offset butterfly valve. It offers more benefits compared to the zero offset and double offset butterfly valves. It can take up to 1200°F in heat or 1,480 PSI of pressure.
The design of this high performance butterfly valve is advanced compared to the other two. Triple offset butterfly valves handle high pressure, offer lower emissions, and are built to suit various environments.
Hardened materials like Stellite and layers of graphite sandwich together to form a laminated multilayer seat. Packing is adjustable and allows contact between a disc torqued into a round seat (which makes it bidirectional).
It’s ideal for applications that need a tight bubble shut-off, soft seating (hard sealing surfaces with zero leakage) or a metal seat (rated leakage) and high temperature tolerance.
The design is similar to the double offset high performance valve with the two offsets situated in the center. The third offset is cam action with right-angled conical sealing. These metal sealing components do not make contact until its final point. This makes it frictionless by design to allow for repeatable sealing and greatly extended valve life.
Triple offset butterfly valve features:
- Higher life expectancy – Designed to eliminate deformation and friction (unlike zero and double offset design).
- Integrity and reliability – High Safety Integrity Level ratings.
- Withstands higher pressure and temperature applications – Metal to metal/graphite sealing plus a bubble-tight shut off. This makes it ideal for controlling or throttling applications.
- Cost effective – Because of reduced materials and weight compared to conventional valves.
- Designed for minimal maintenance – Replaceable seat/seal and disc/stem components.
- Fire safe – Automatically seals in the event of excessive heat or a fire event when the graphite seat is destroyed.
- Low fugitive emissions – Due to more precise quarter-turn technology.
- Particle ingress elimination – Due to no cavities between sealing components (unlike zero and double offset design).
Valve Applications
Double and triple offset butterfly valves are similar in application, but the latter meets more specific needs. The triple offset butterfly valve is suited for tight situations, tougher applications, easier maintenance, high temperatures (including fire), and what requires a long life cycle. Other benefits include optimal torque transmissions and cost-savings (in some cases).
Special requirement applications are:
- Refineries (such as oil)
- High-pressure steam operations
- Chemical plants
- Offshore oil and gas
Contact Butterfly Valves & Controls Today for Your Butterfly Valve Needs…MADE IN TAIWAN
The three butterfly valve types are designed to adapt to a wide range of applications from the simple and low risk to the complicated and volatile. The design differences between high performance vs resilient seated butterfly valves stem from the intended use. They are manufactured according to the exact performance specifications of each industry and operation.
Which butterfly valve seems to be the right one for your systems and processes? Let Butterfly Valves & Controls confirm your best guess by contacting us. We’re dedicated to helping you find the precise fit for your butterfly valve needs.
No Comments